CONSTRUCTION PAGE -- SARDINE CARRIER 53 DEADRISE MOTORSAILER

SAIL PLAN FOR REUEL PARKER'S CRUISING RETIREMENT HOME
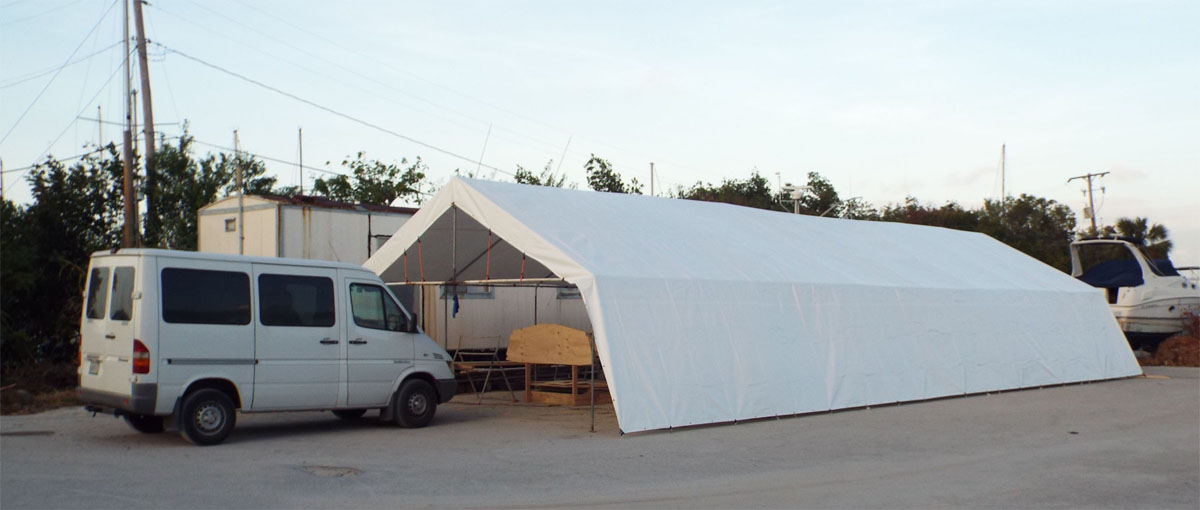
Parker Marine at Riverside Marina, in Ft. Pierce, FL--The big tent,
December
2016
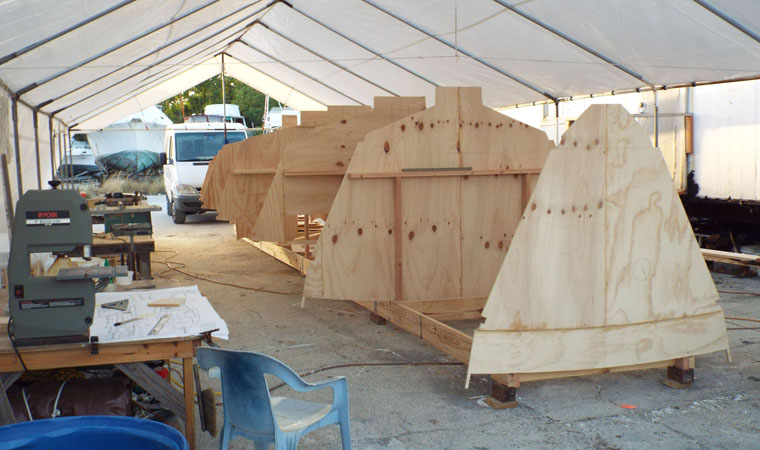
The strongback bolted to the asphalt, with diagonal braces and 2x4
stanchions for mounting
bulkheads
The bulkheads, lofted from the table of offsets,
erected on the strongback--note 2x4
stiffeners
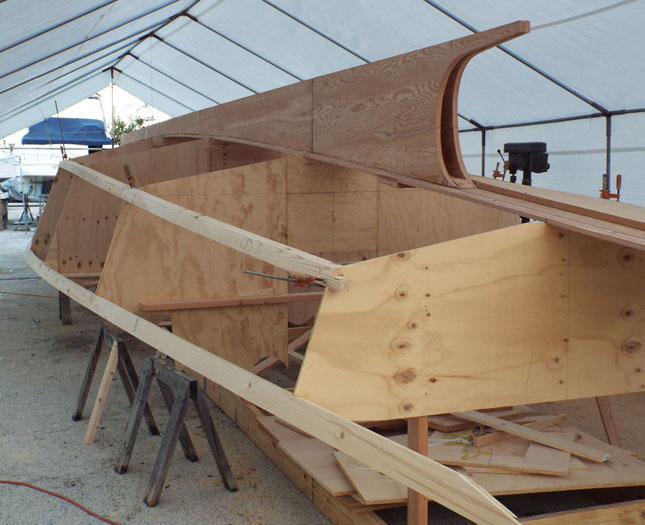
Longitudinals: sheer clamps, beam
shelves and chine logs scarfed
full-length
Longitudinals in place, with the box keel started
using 1" marine
plywood
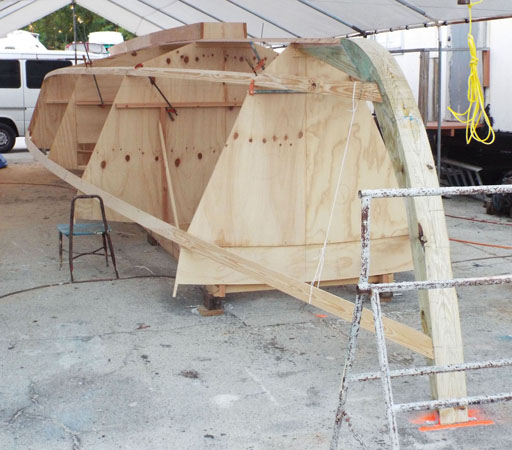
The apron/forefoot/knee assembly from 6x6 Wolmanized pine
In
place
on the frame--beam shelves, sheer clamps and chine logs are
installed--box keel started
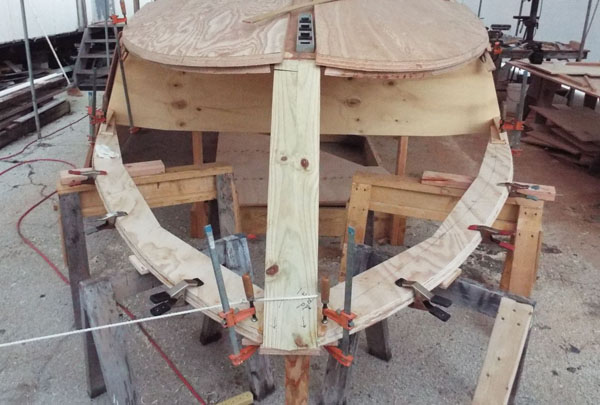
Forming the "flat-frame" structural members of the duck tail
stern
The rope leading
left is holding the 6x6 stern post plumb while the epoxy cures

The duck tail stern planked from two layers of 3/8" marine plywood,
scarfed into the 3/4" plywood topsides planking. Bottom planking is 1"
marine plywood.
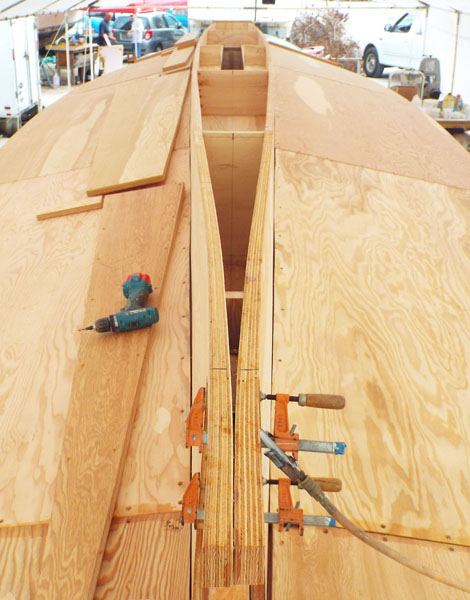
Planking the hollow box keel--filling in the propeller aperture (left);
preparing to plank the bottom (right)
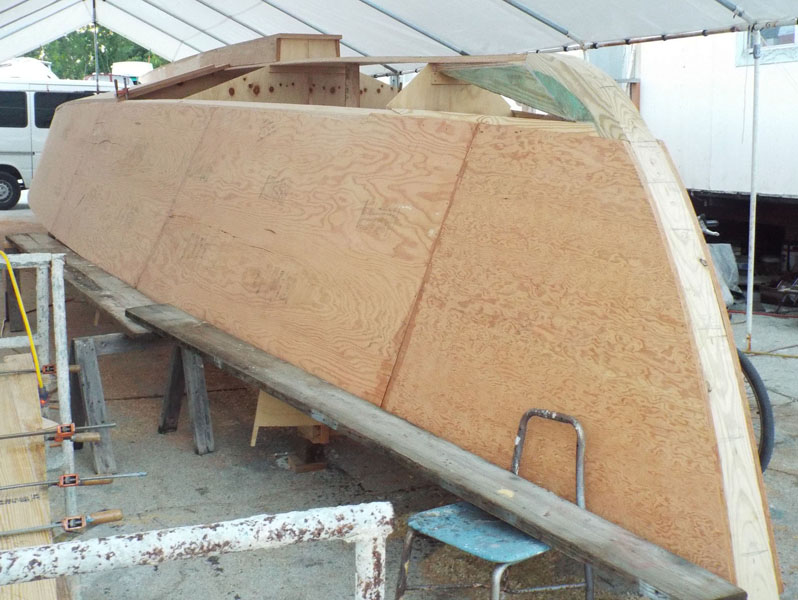
The
box keel
planked
Topsides
planking finished; bottom planking approaching the bow--due to
twist, the remaining bottom planking consists of two laminates of 1/2"
plywood
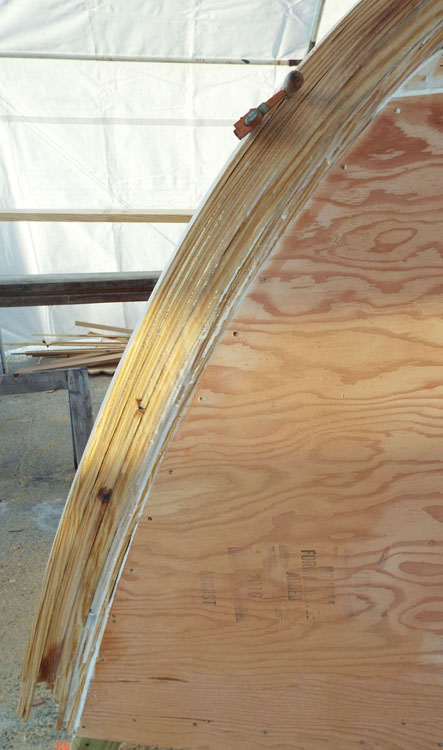
Planking
finished; note the transition from overlap to butt joint along
the chine
Starting the outer stem laminations using 3/8" x 5 1/2"
strips of yellow pine Finishing the outer stem--the
bow structure is over 10" thick--very strong!

The finished hull, ready for Xynole-polyester fabric and epoxy; note
the step scarf of outer stem to the solid yellow pine gripe keel; note
taped and faired butt joints
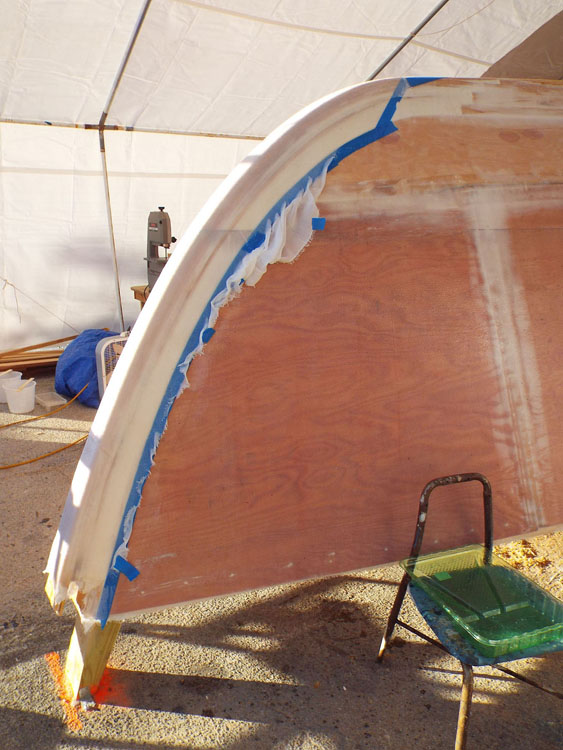
Xynole/epoxy covering the hull--the starboard side is finished,
and the port side has just been wet out
Layers overlap the keel and
stem
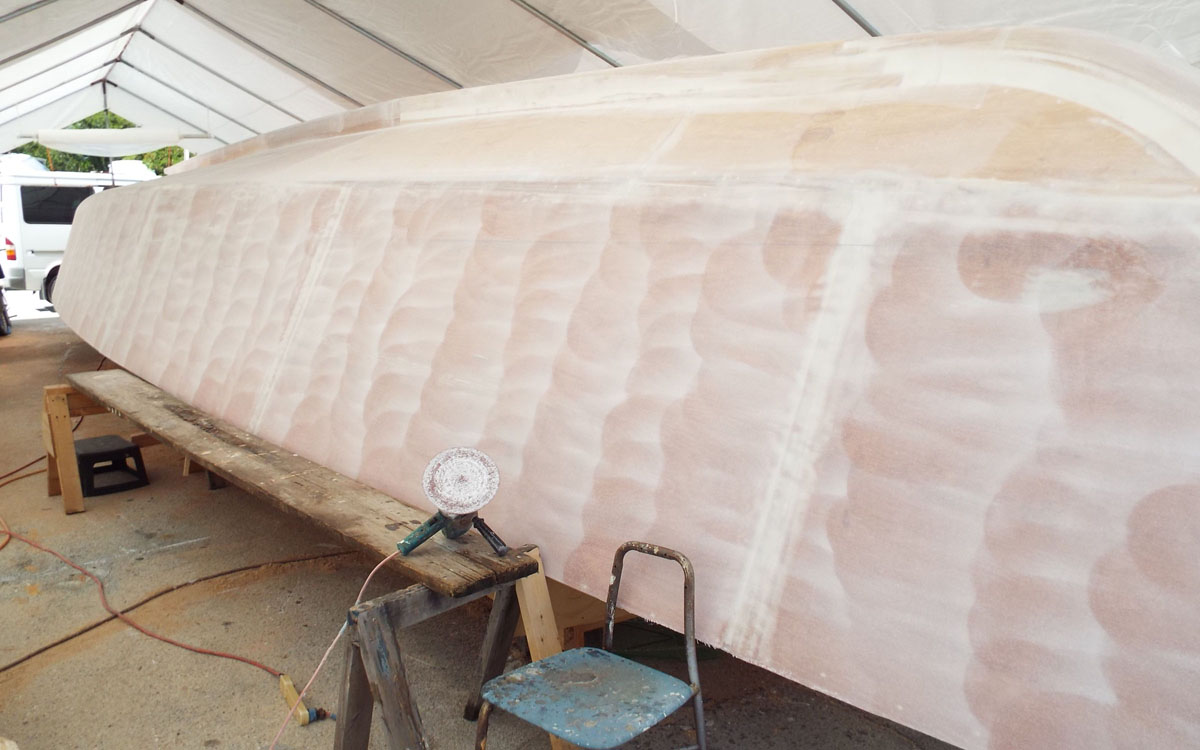
The first layer of Xynole/epoxy is finished, including two layers over
the keel and stem, and the hull has been sanded to #60 grit using the
low-speed Makita body grinder with thick 8" soft pad

After cleaning the sanded hull, a second layer of Xynole/epoxy is laid
below the boot top--eight layers are laid over the stem and keel

The sanded hull has been primed with high-build sandable epoxy primers
(two coats), and turning wheels are built in place

The very strong lifting eye is located near the center of the
hull
Bill Smith is setting up the
gantry's chain falls
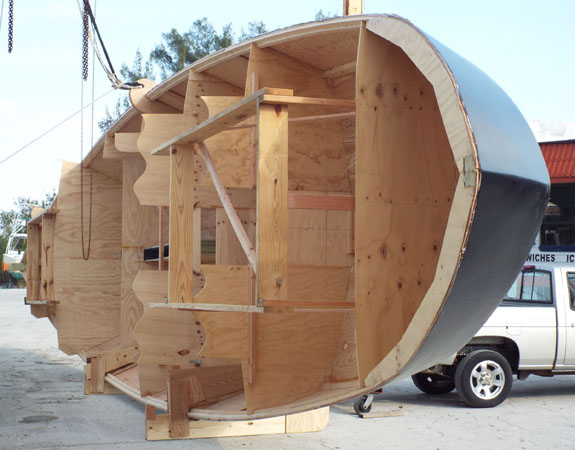
Starting the turn--we had to beef up the turning wheels in
situ!
Half
way--the next part is tricky!
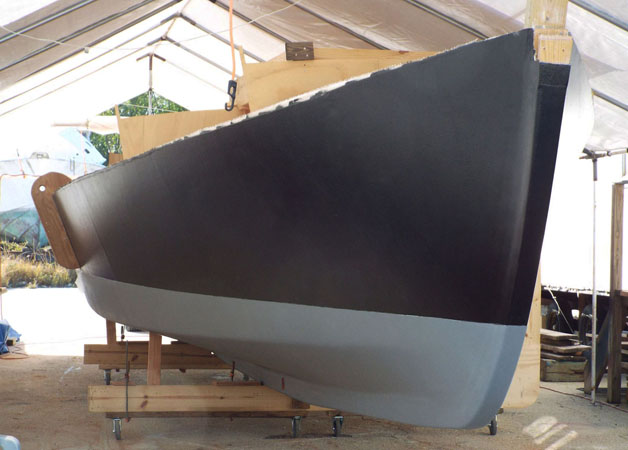
Almost! We
used both chainfalls to control the drop--working at their upper
limits!
Right-side-up at last--back in
the tent

After removing strongback components and cleaning up the interior, I
saturated it with penetrating epoxy and began installing deck structure
A cabin trunk carlin with
mortises for side deck beams glued and epoxy
sealed
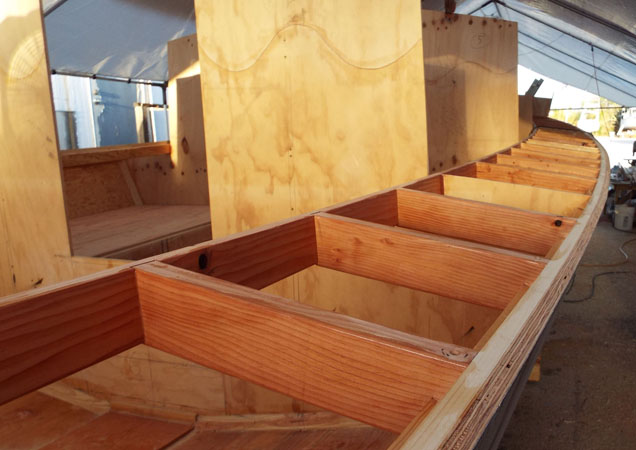
Using a router template for beam- and hatch carlin-end
mortises
Douglas fir side deck beams
glued and sealed in place

A fuel tank baffle being Xynole/epoxy covered, starting with the
corners
The
port side fuel tank into which the baffle will be placed

Cockpit well deck scupper--from outside (left) and inside (right); the
hole (upper left) is for electrical conduit
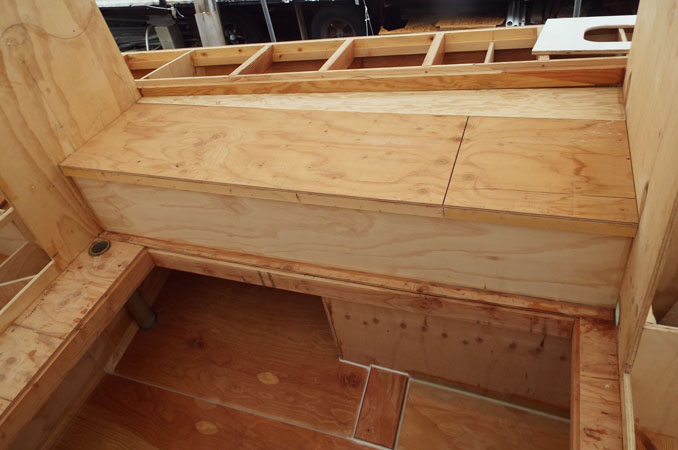
Cockpit well deck--scupper (left), fuel fill (top) & fuel tank vent
(right)
Cockpit
showing 3" fiberglass scupper (left), and seat/locker over port
fuel tank
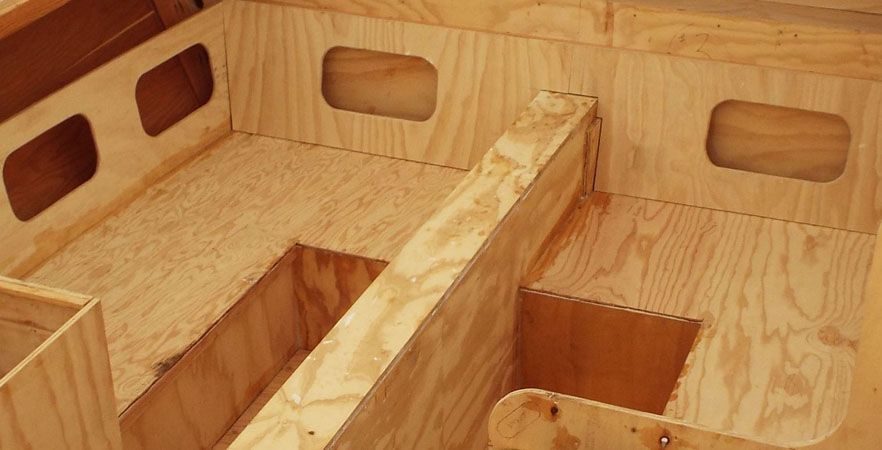
Starboard-side water tank with baffles, Xynole/epoxy covered and
painted with epoxy potable-water tank
coating
Settees
in the main saloon built over the water tanks--centerboard
trunk
between
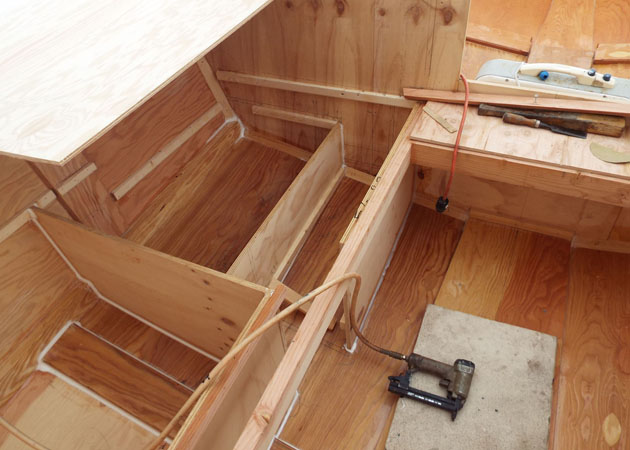
The main companionway
steps from the
cockpit
The cockpit--holding
tank and shower well (upper left); starboard fuel tank (lower left);
engine compartment (right)
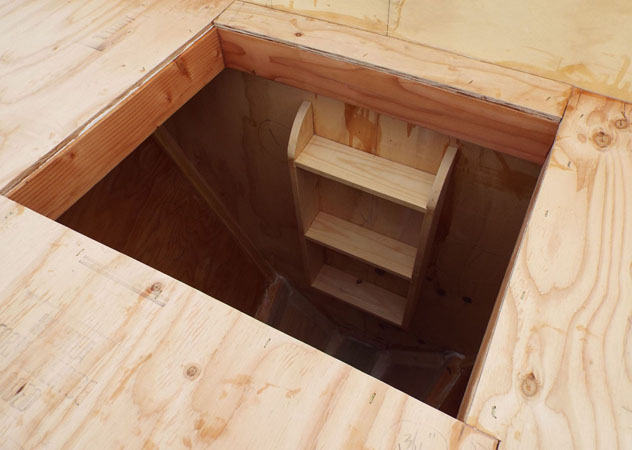
The
fore deck and forepeak hatch
opening
Fore peak (chain & rode locker)
and access ladder
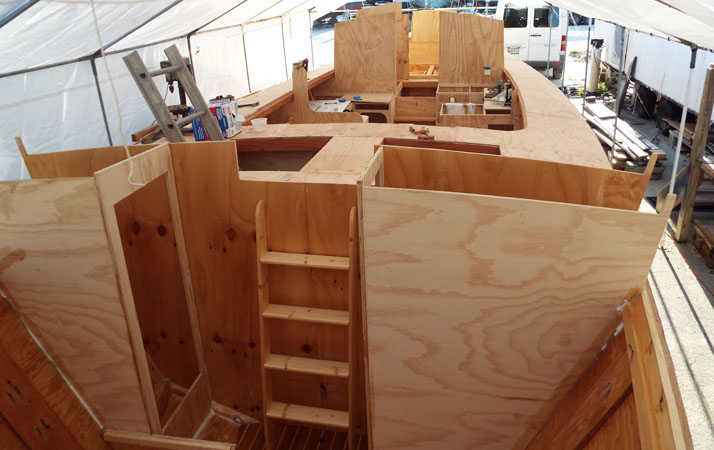
The forepeak hatch coamings and hatch frame glued in
place
The foc's'le ladder and cabinets
roughed in
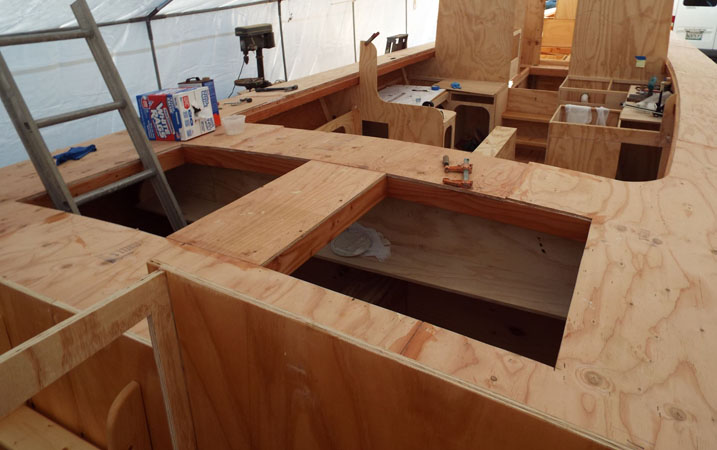
The
foc's'le V-berth framed with removable cabin
sole
The cargo hold hatch
openings
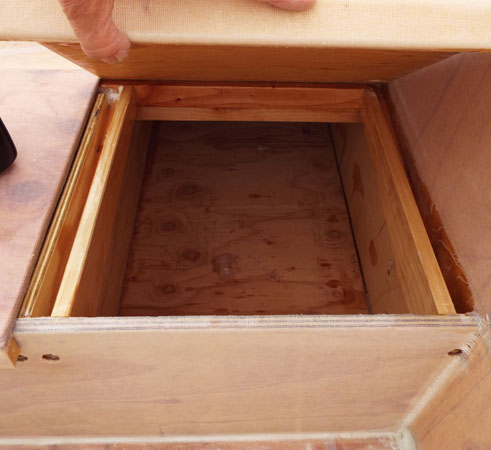
The cockpit/pilothouse: starboard helm seat/locker (left); engine
compartment and port seat locker
(right)
Forward port seat locker open showing drain
channels
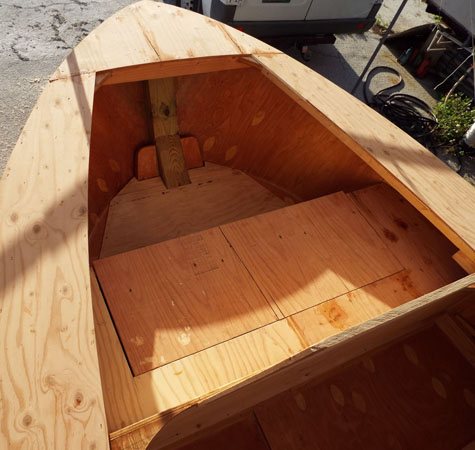
The aft sleeping cabin showing hanging lockers, drawer boxes and
removable cabin sole
The aft cockpit showing
bench
seat/locker
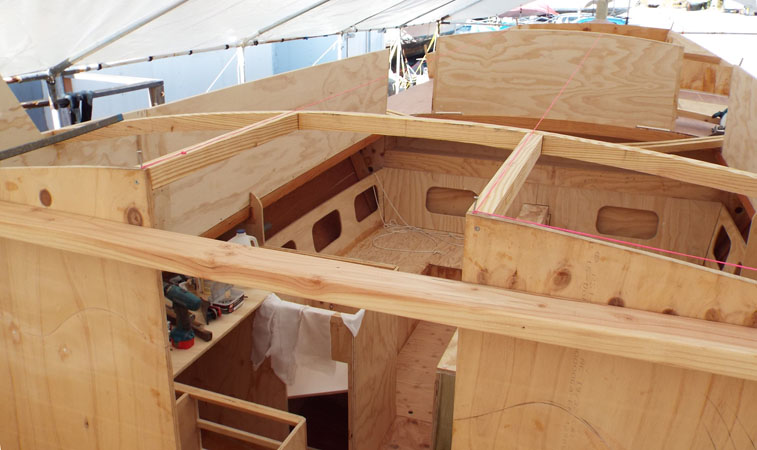
Using the coachroof beam template to cut the tops of cabin ends; decks
covered with
Xynole/epoxy
Starting the coachroof frame for the main saloon (note 2x4
stiffener)
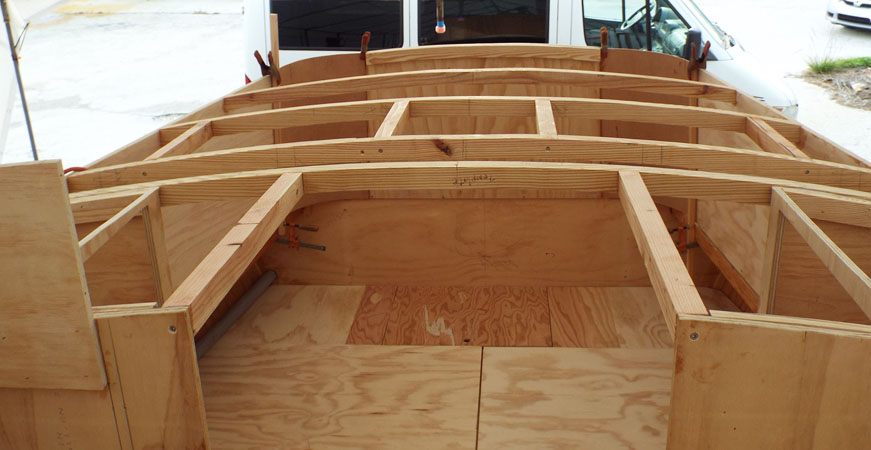
A first laminate for a cabin corner using 3mm Meranti
plywood
The aft cabin coachroof frame, with
rounded corners aft
The main saloon coachroof in frame--the 2x4s on top hold the beams in
alignment while the headliner is installed
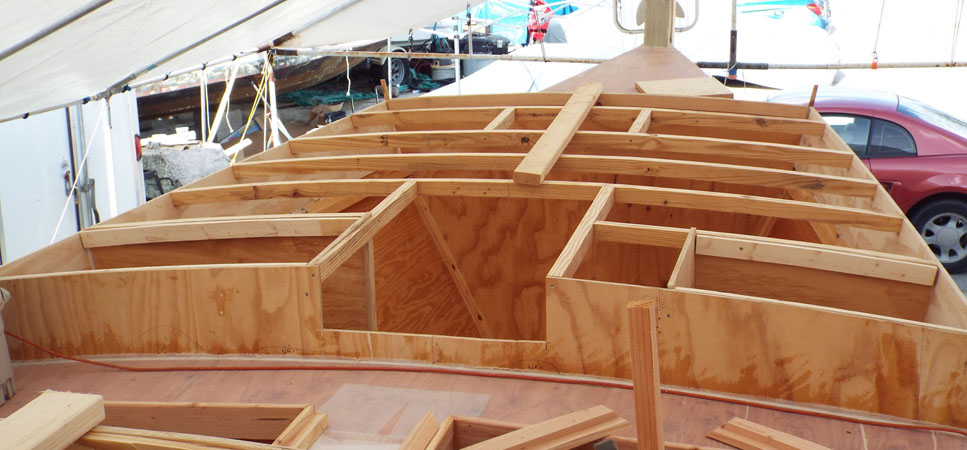
The raised fore deck over the foc's'le--beams here are 2" high
(coachroof beams are 1 3/4" high), and crown is the same as for the
decks
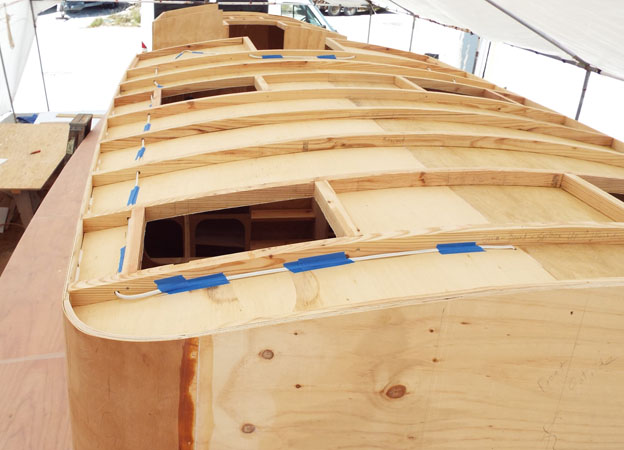
A cabin trunk corner laminated from six layers of Meranti
plywood
Headliner installed for the
main saloon--pre-wired for overhead lights
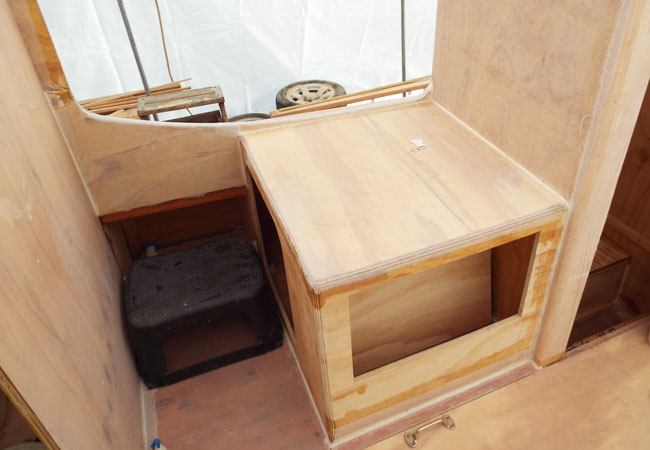
The cockpit/pilothouse
showing the port side seat/locker and engine hatch; coamings are
doubled in thickness
The Cockpit helm seat on the starboard side; propane
bottles under outboard; tool box inboard
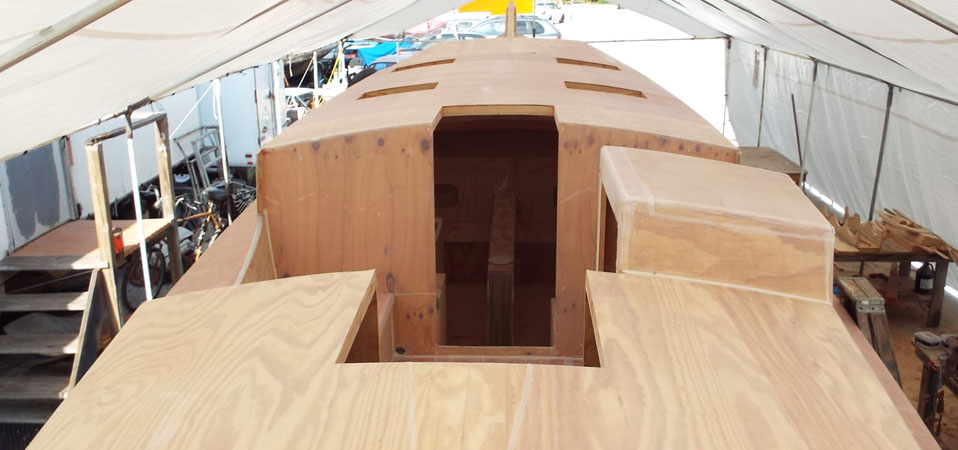
The main saloon with pre-painted headliner installed--Galley to port,
office to starboard, settees forward
View
forward from the aft cabin coachroof--the outside head/shower
compartment is to starboard--all Xynole/epoxy covered

Early May, 2017 -- The structurally complete boat is shrink-wrapped for
the brutal south Florida summer; labor time was 24 1/2 weeks, and
materials costs were just under $16,000
* * *
* *
I returned to Riverside Marina on
Sunday, October 22, 2017. My shrink-wrap cover
had been blown off the boat numerous times, and my boatbuilding partner
Bill
Smith had replaced it as best as possible. He had to pump a lot of
water out of
the hull, and added plywood covers where necessary.
Then Hurricane
Irma
arrived.
When I opened up the boat,
removing the tattered shrink-wrap
and Bill’s plywood, I found water inside numerous compartments. The
engine room
was completely flooded, containing perhaps 100 gallons of water. There
was
extensive mold everywhere, and damp plywood under the water in places
even though
everything had been sealed with penetrating epoxy. I used my shop-vac
to
suck out most of the water, but I had to use a transfer pump to start a
siphon in
the engine compartment. It took over an hour to drain.
My financial situation at this
stage of my life was a
disaster. I was completely broke, and running into debt—I had to borrow
thousands of dollars just to keep going. I had two options: One—get a
reverse
mortgage and establish a line of credit so I could keep building;
Two—try to
limp through the
winter with
rent money (I had tenants moving into my house on
December 1st. ). Fortunately, I also had some boatyard work
lined up.
It turned out that my income is so pathetic that I don’t qualify for a
reverse
mortgage, so that option dropped out.
During my previous summer in Maine,
taking advantage of my barn
and all my industrial milling tools, I had pre-made all of my
trim—deckbeam
covers, fiddle rails, seam trim, bunk boards, hatch coaming trim, etc
from a
very large Honduras mahogany timber I had in stock. I milled rock
(sugar)
maple
for my countertops, yellow birch for my centerboard cap, cabinet doors
and
saloon drop-leaf tables, and miles of big-tooth poplar (pure light tan)
for my
ceiling planking. All but the mahogany came from my own trees.

Mahogany trim, epoxy sealed and varnished, ready to be installed in my
interior
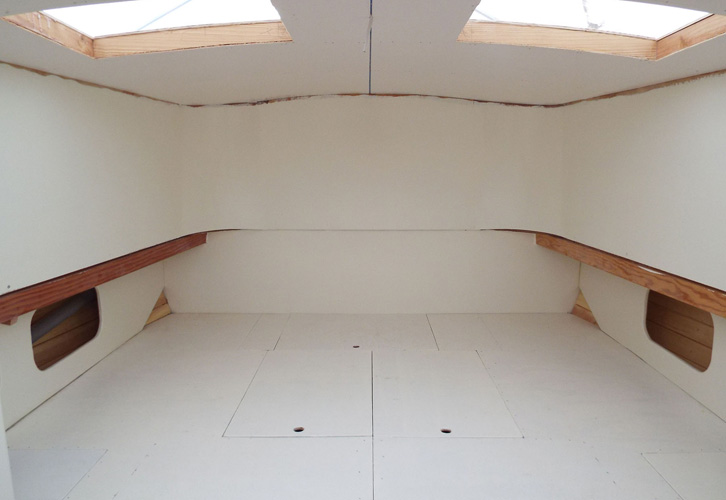
I laminated rock maple on all my counter
tops
The aft sleeping cabin (master's cabin) roughed in; The aftermost
removable panel accesses the steering gear

More mahogany trim--bunk boards, fiddle rails, coachroof beam caps, etc
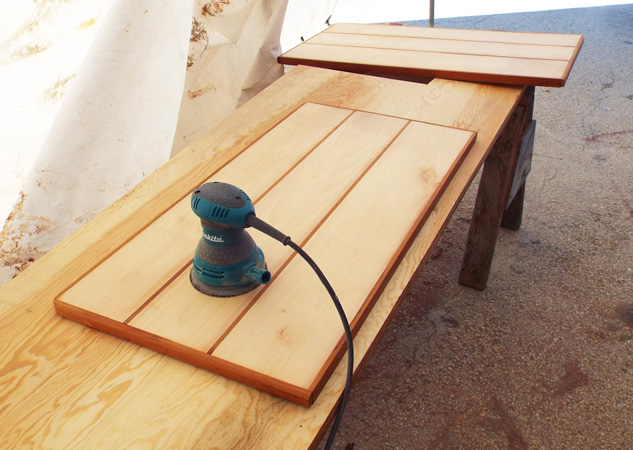
Drawers with beveled yellow birch faces
The drop leaf tables, made from yellow birch and mahogany

Using a heat gun to bend mahogany corner trim
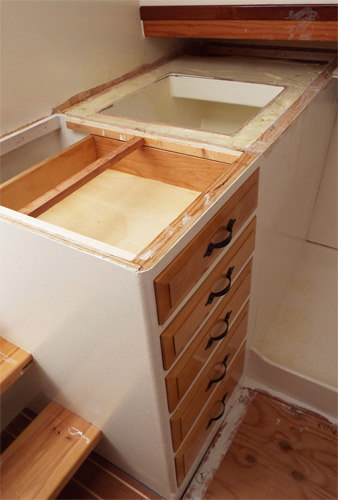
Pouring the
closed-cell polyurethane foam for the refrigeration
compartment The
mess trimmed (using a machete); Galley drawers in place
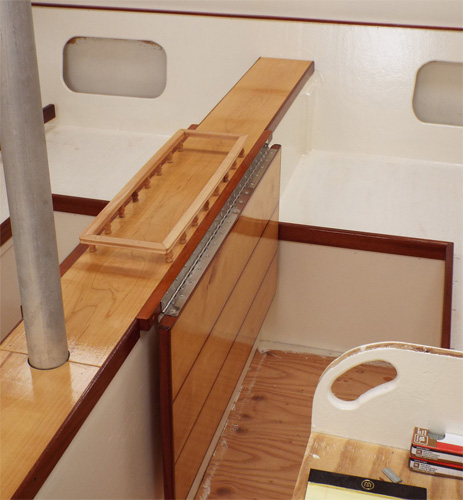
The office drawer and
cabinet
The centerboard cap with drop leaf tables; the pipe is for the
centerboard penant
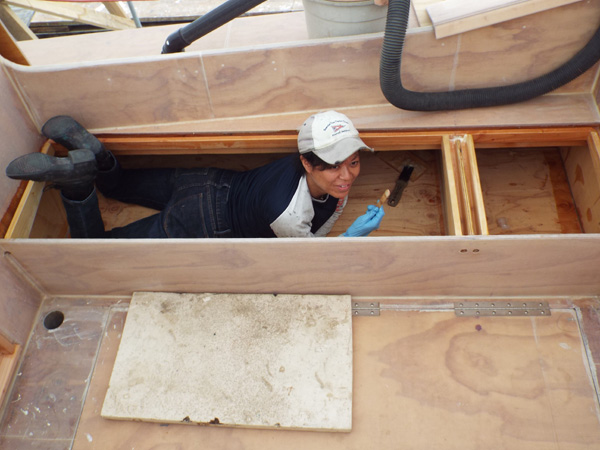
The Nav desk, hinged to
access space beneath for drafting & nav
tools
My brief helper (six days) Chure filleting compartments
too large for me to get into
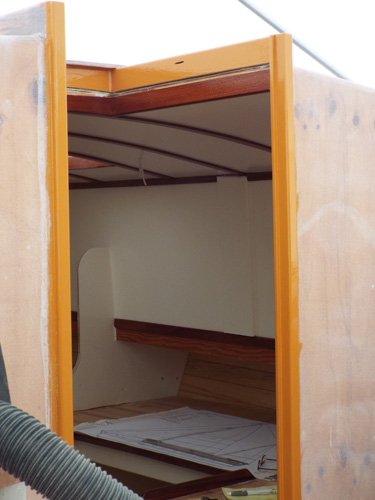
Cockpit helm seat locker--my mechanic's tool box will be installed on
tracks in the lower
opening
Companionway to the
saloon
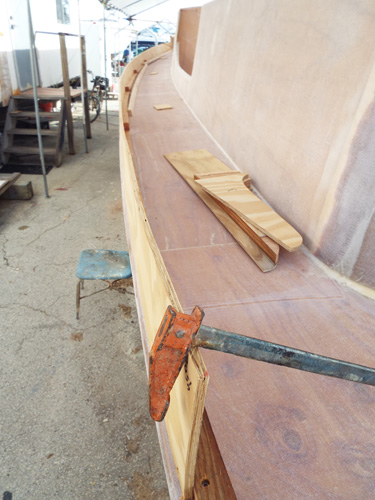
Starting the A-frame
bulwarks--the solid wood base--note the "bridges" for the
scuppers
Bulwarks--the outer laminate of 3/8" plywood installed
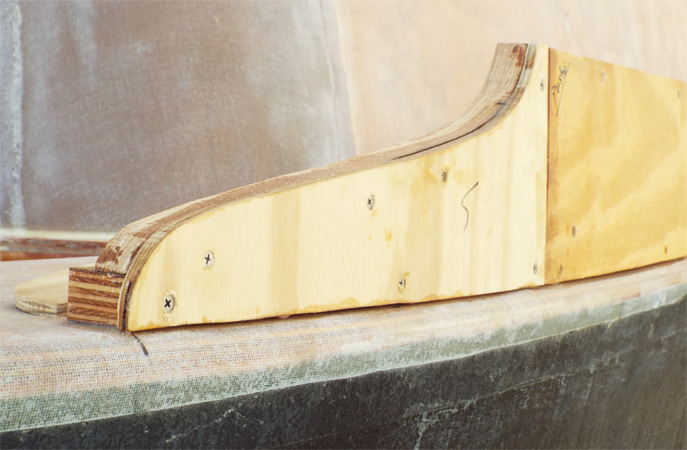
Installing the upper bulwark
cleat
The aft
end of the starboard
bulwark

The bulwark where it rises proceeding forward to enclose the raised
foc's'le
deck
The bulwarks at the bow prior to installing the inner
laminates
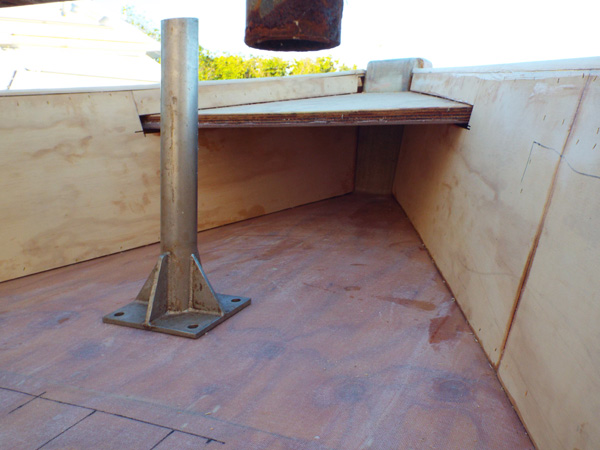
The inner
bulwark laminate installed and the solid cap started
The inner laminate
installed around a shelf of 1" marine ply to support the windlass
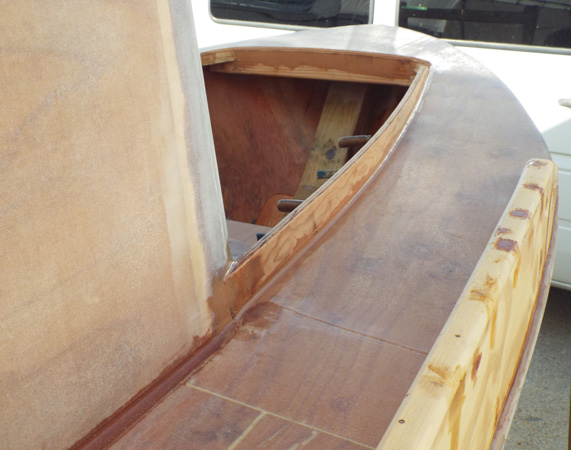
The bulwarks finished from outside (forward)
The bulwarks aft; The aft cockpit coamings being
installed
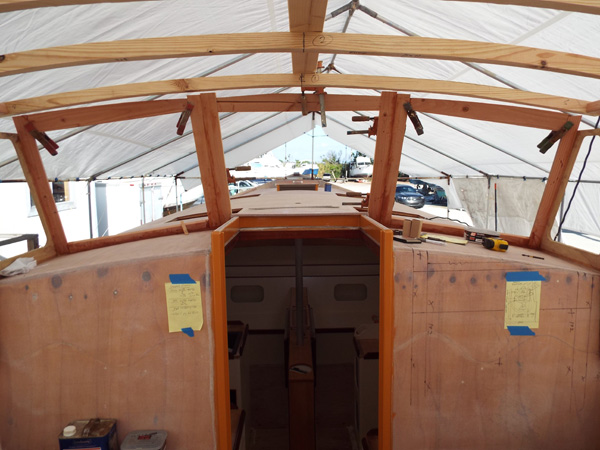
The pilothouse hardtop in frame; Bulwarks ready for Xynole/epoxy
The windscreen in frame

The pilothouse in frame from the
front
The foam-core hardtop structurally complete, ready for Xynole/epoxy;
The small stock by the windows is for the opening window frames
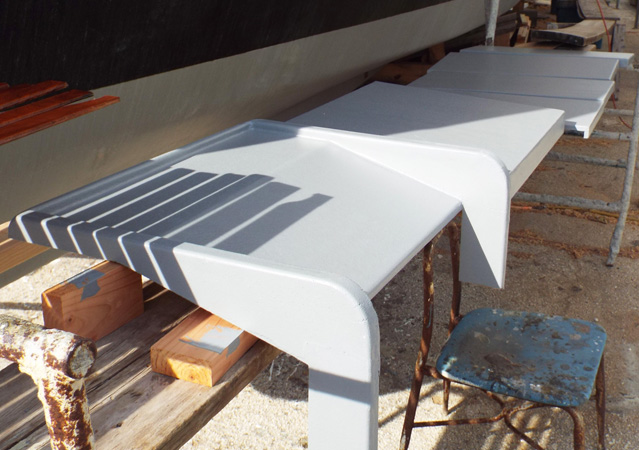
The Hardtop in primer, with mahogany deckbeam trim; The mizzen
tabernacle
Helm console and
hatch covers in primer
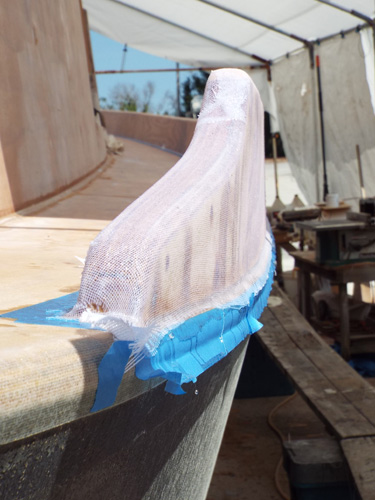
The aft cockpit and seat locker
The
starboard bulwark end, Xynole/epoxy covered
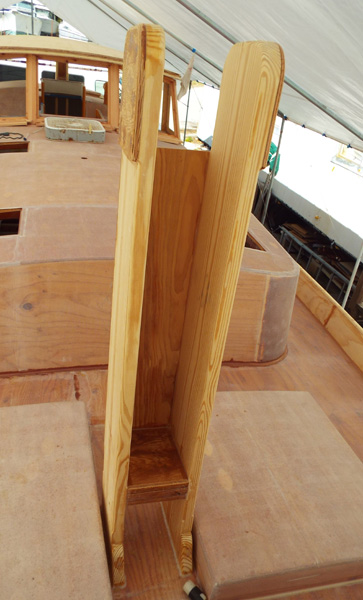
The mainmast tabernacle (two views)
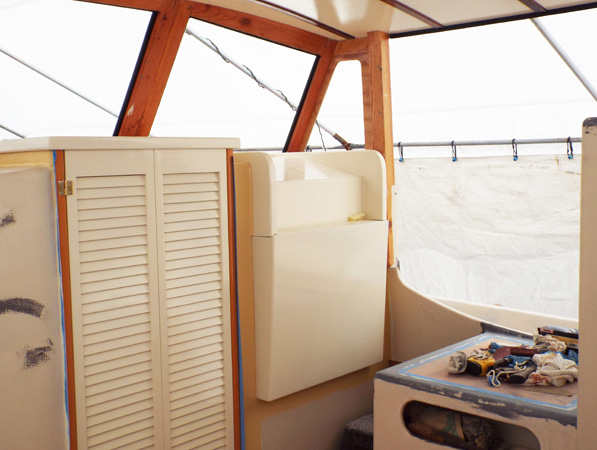
Louvred
companionway doors under
construction
Doors and bi-fold hatch cover installed for the saloon companionway;
Helm station installed
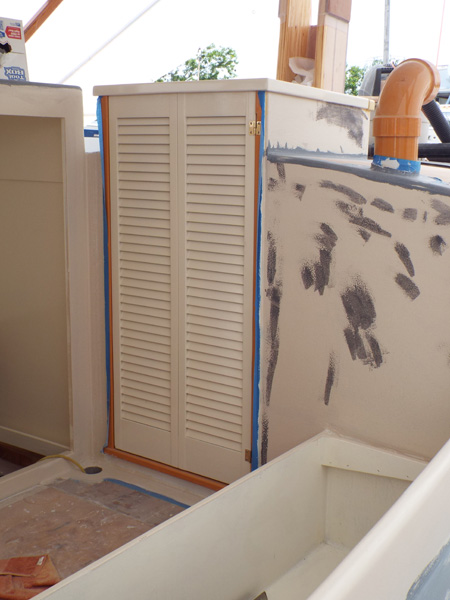
The hardtop painted and trimmed; The black perimeter channels are for
vinyl side/back curtains to enclose the
pilothouse
Companionway doors and
bi-fold hatch cover for the aft cabin
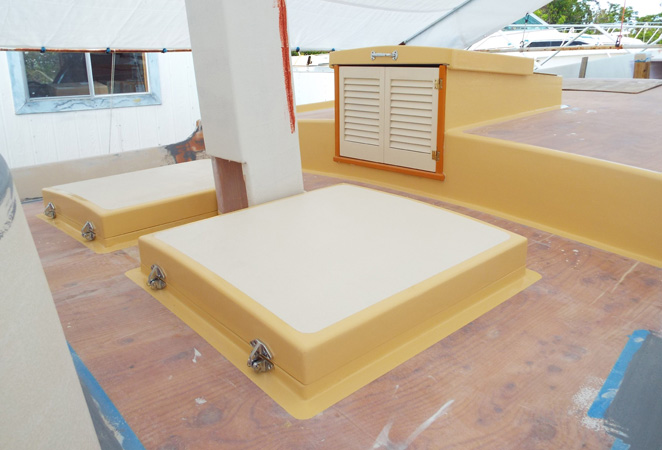
The opening window frames in
primer
The bridge deck with painted cargo-hold
hatches and focsle companionway
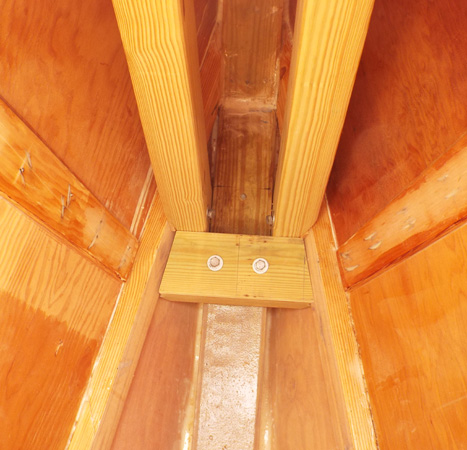
The well deck forward; Forepeak hatch, Mooring bitts; Stays'l boom
pedestal; Windlass
shelf
Mooring bitts stepped & bolted to the chine logs
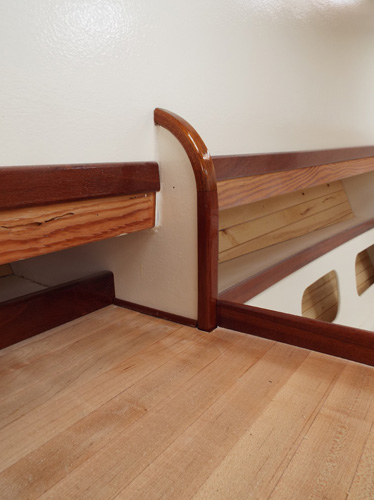
The
refrigerator
lid
Galley trim
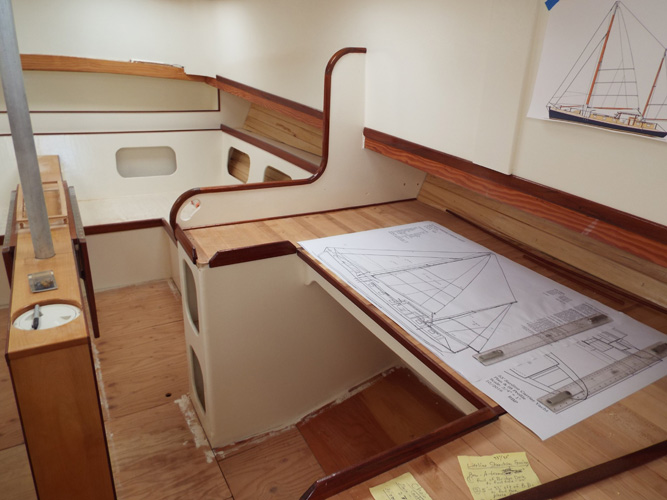
The saloon--view forward from the nav station (starboard)
The nav station/office (starboard)
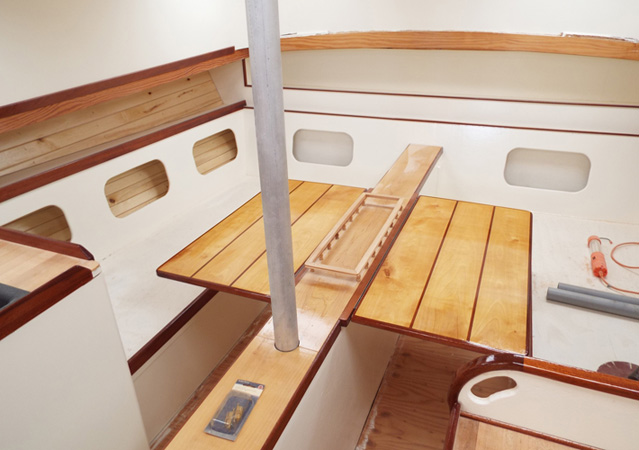
The saloon--view forward from the galley
(port)
The saloon--drop-leaf tables
open; I installed 3/4" foam insulation behind the poplar ceiling
planking
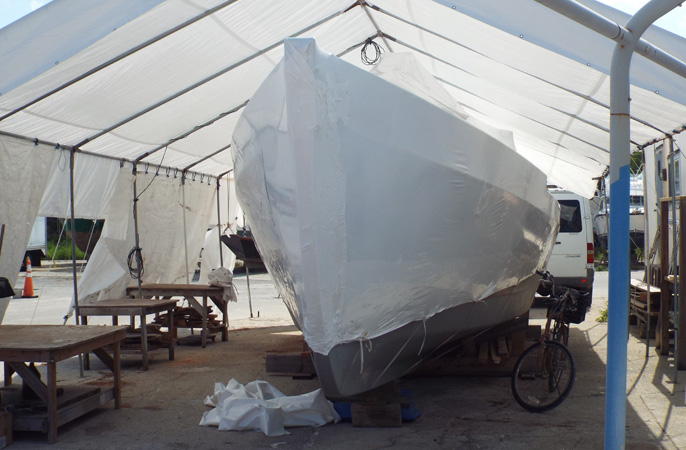
The structurally complete boat in primer
The boat shrinkwrapped for the 2018 summer season (much
more carefully than last time!)
Time elapsed was six months, and total expenses
were $8,500. Total work time elapsed was now one year, and total
expenses
were now $24,500.
Labor is more difficult to pin down, as I
didn’t record my
hours. But it is safe to estimate my labor for these first two
six-month work
periods to be over $100,000, for more than 2,000 hours. Unlike most
people, I
work seven days a week… until I set sail!
“You got to have a dream…
if you don’t have a dream…
how you gonna have a dream come true.”
—Bloody Mary, in South
Pacific, by Rodgers and Hammerstein