CONSTRUCTION PAGE -- SEA BRIGHT 14
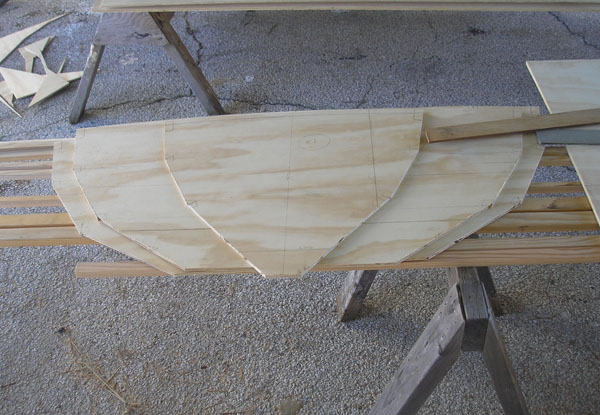
Use
the
Table of Offsets and the Lines Drawing to loft bulkheads onto
Plywood
The bulkheads
cut out, after subtracting scantlings thicknesses--from 3/8" Arauco
pine
plywood from Chile
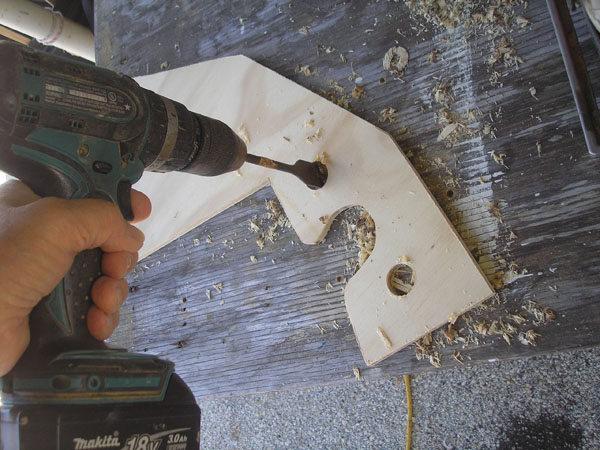
Bulkheads divided by the centerboard trunk are joined by a piece
of scrap plywood
Drilling holes in
bulkheads for stowage of oars, boathooks,
etc.
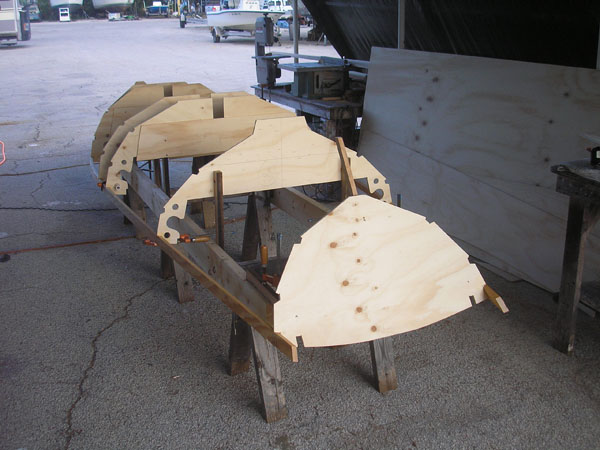
The
strongback,
made from sawhorses and
2x6s
The bulkheads set up on
stanchions erected from the strongback--the inner transom is supported
beyond the strongback
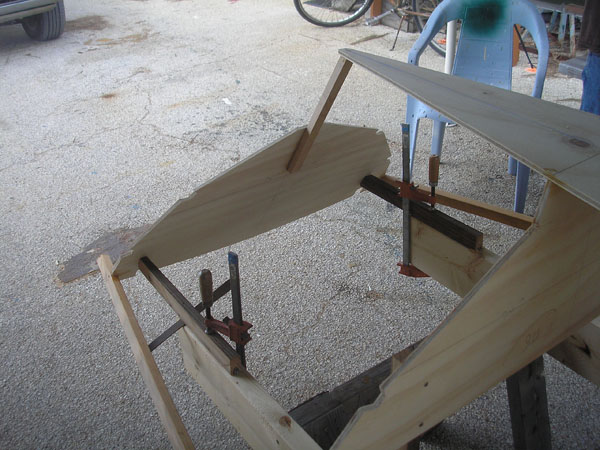
The
apron/forefoot/knee
assembly ready to add to the
frame
The inner transom braced from the
strongback with sheer clamps and keel bottom attached
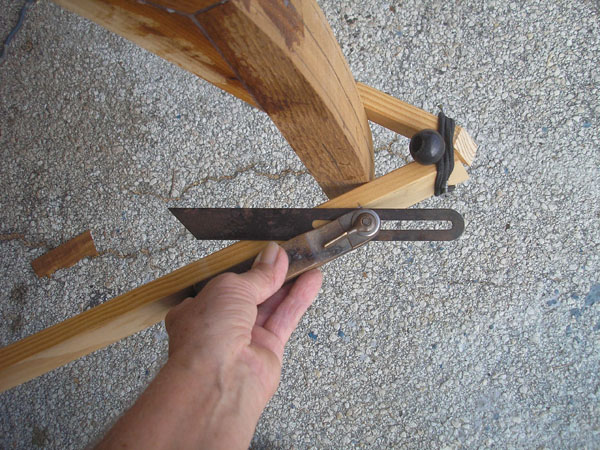
The
apron/forefoot
assembly mounted on the
frame
Using a bevel
square to determine the cut angle for the sheer clamp to apron joint
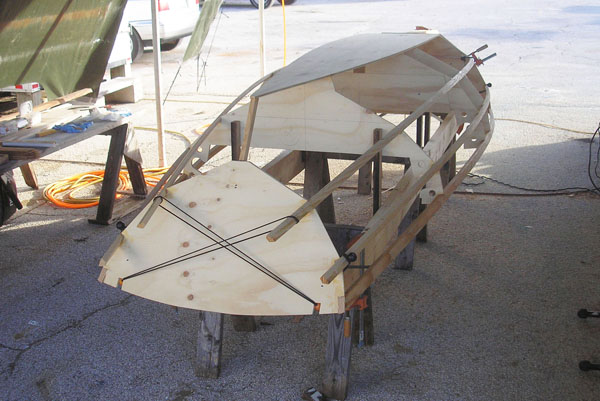
Sheer
clamps
joined to the apron with breast
hook
The hull in
frame with sheer clamps, chine battens and inner keel-plank bottom
installed
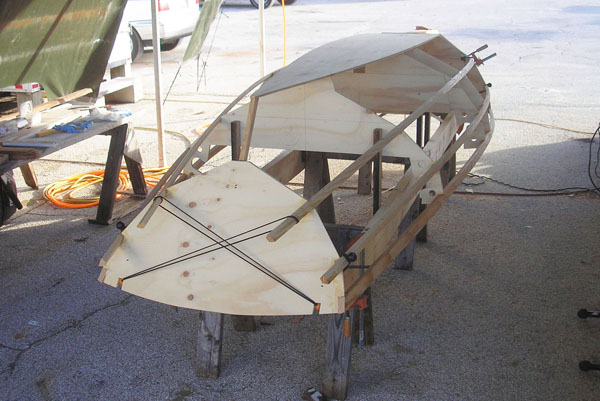
The frame with all longitudinals finished except the forward half of
the inner keel-plank bottom (view from forward, left; view from aft,
right)
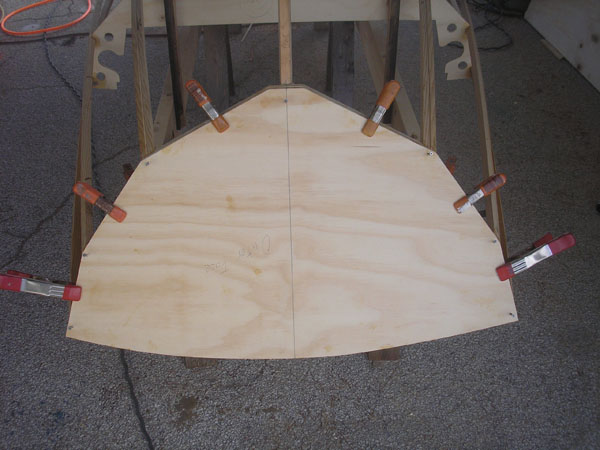
Bow frame detail
Transom outer
layer being laminated over the inner layer
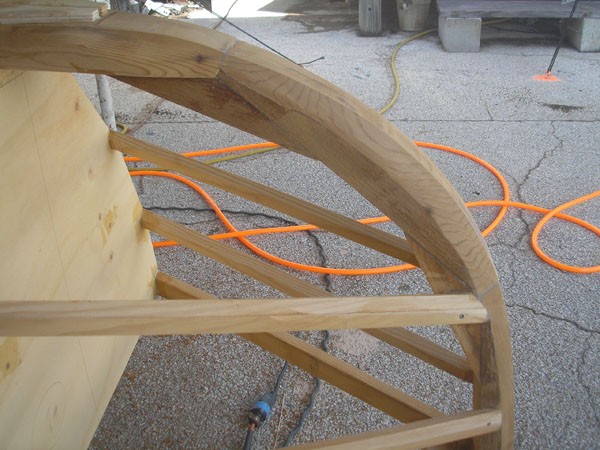
Using a low-speed body grinder to bevel the chine logs for
planking
The apron
sides beveled for
planking
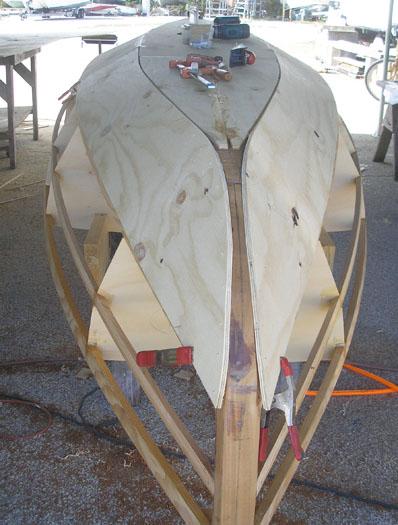
Garboard planks going on (stern view left; bow view right)

Box keel sides going on
Middle
and
sheer strakes going on
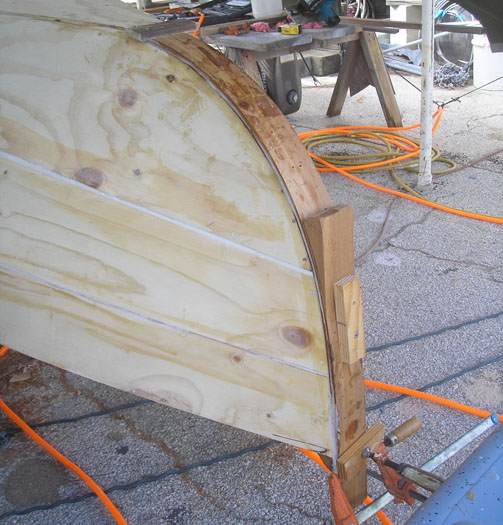
The planked hull, ready for
final keel-plank bottom layer
The keel-plank finished; first outer stem
laminate going on
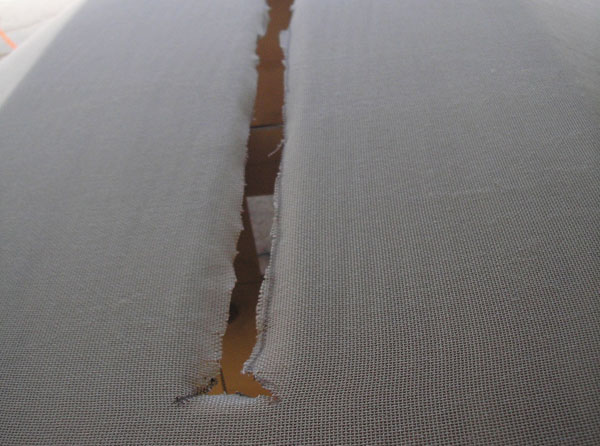
Applying Xynole-polyester fabric (keel, left; centerboard slot, right)
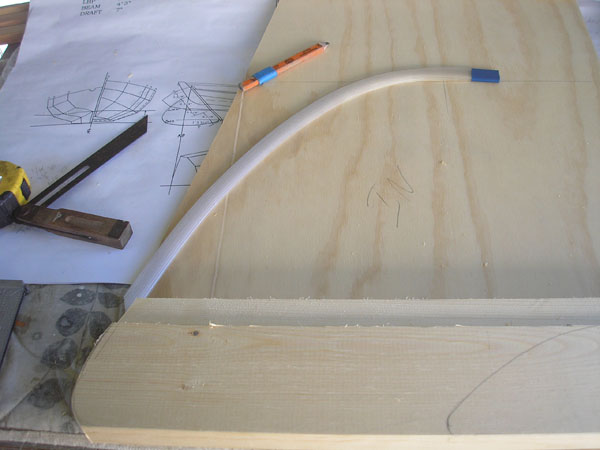
The hull covered in Xynole/epoxy, with two layers on the
bottom and stem
Using a drawing batten to establish rudder shape; note rabbet in post
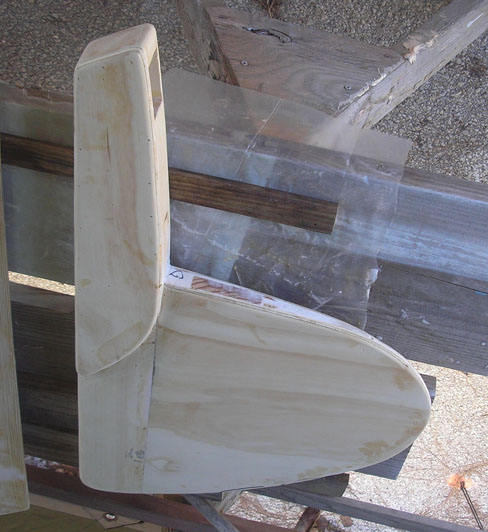
Laminating the rudder halves into rabbets cut in the
rudder post
The finished
rudder with solid core and cheeks for the tiller
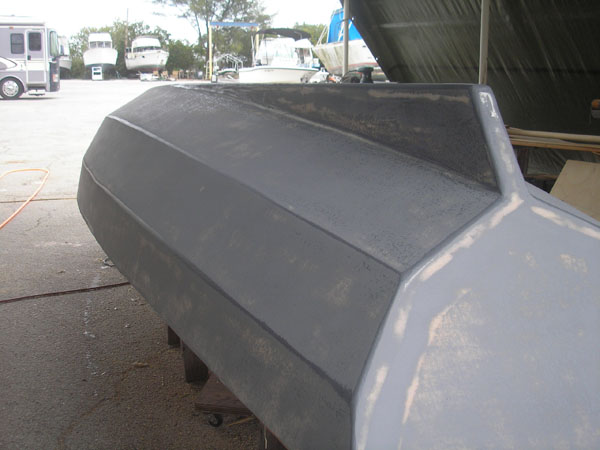
The
centerboard
shaped and
faired
The hull in primer, sanded--note that the
chines must be hand sanded, as a power sander would make them unfair!
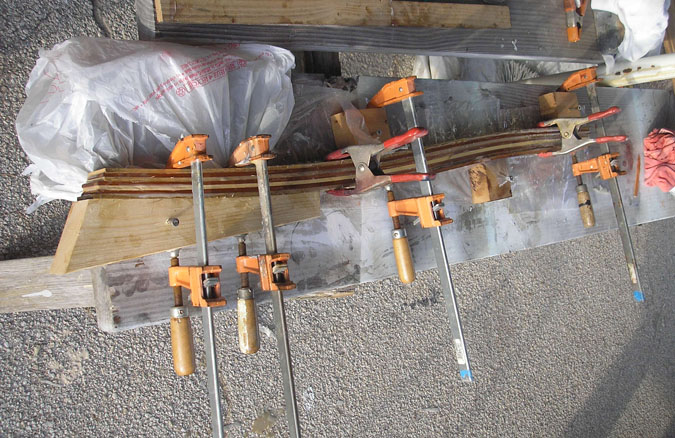
The rudder covered with
Xynole/epoxy
The
tiller being laminated from ash and mahogany
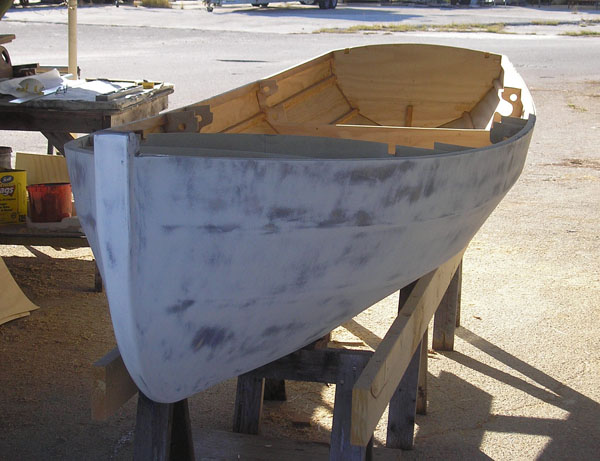
The tiller, shaped, sanded and epoxy
sealed
The
hull
right-side-up, in primer
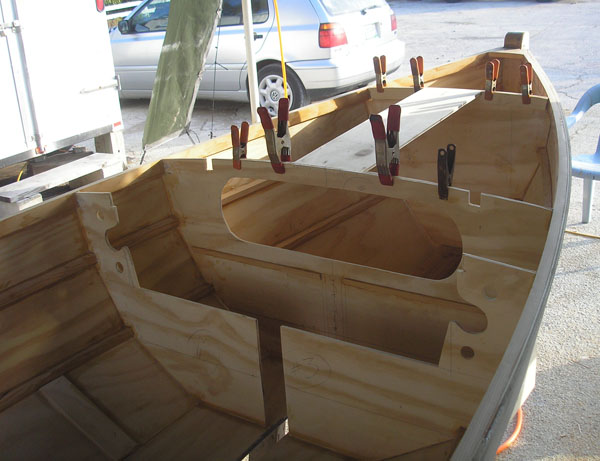
Fitting
the
side deck
carlins
Preparing the foredeck and mast
partner; adding stiffeners to the adjacent bulkheads
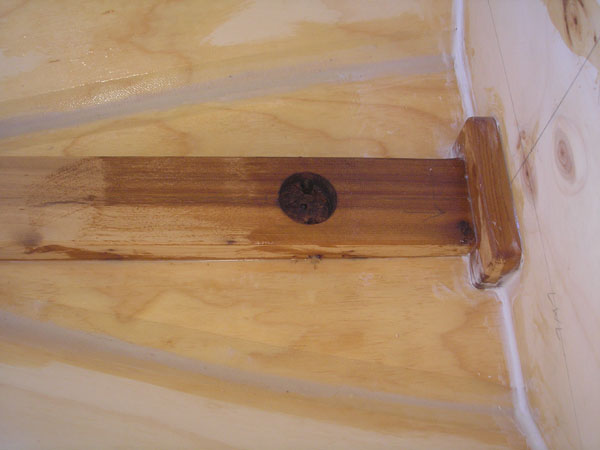
Installing the centerboard trunk halves and
posts
The mast step
with weep holes
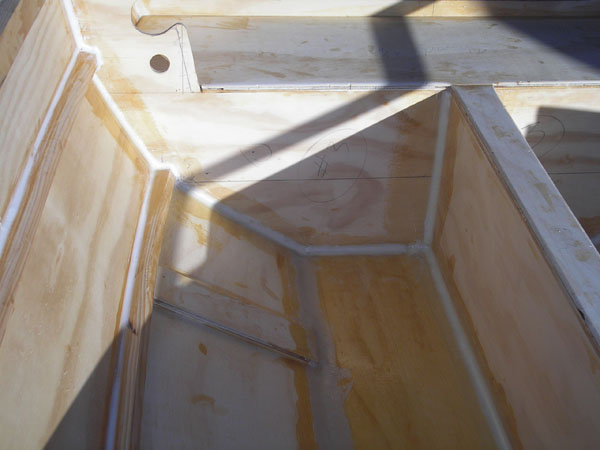
Laying 1" and 3" fiberglass tape directly onto wet
epoxy/Cabosil/microballoon fillets
Wetting
out tape &
fillets
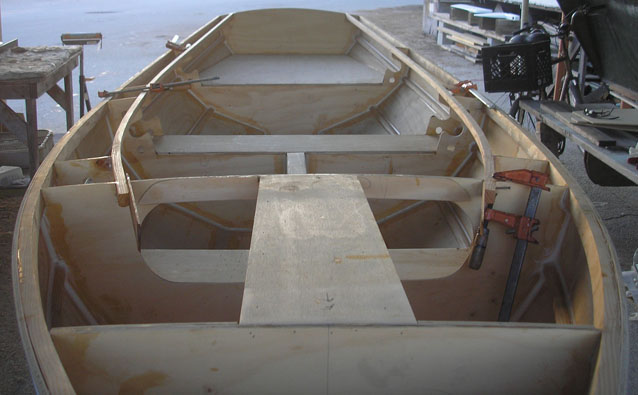
Deck carlins being glued in place
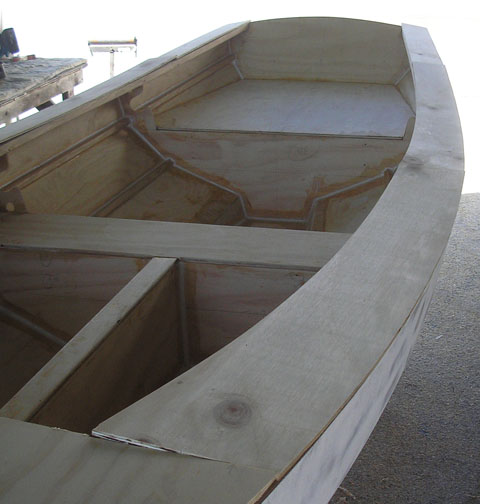
Side deck layout--dry fitting first
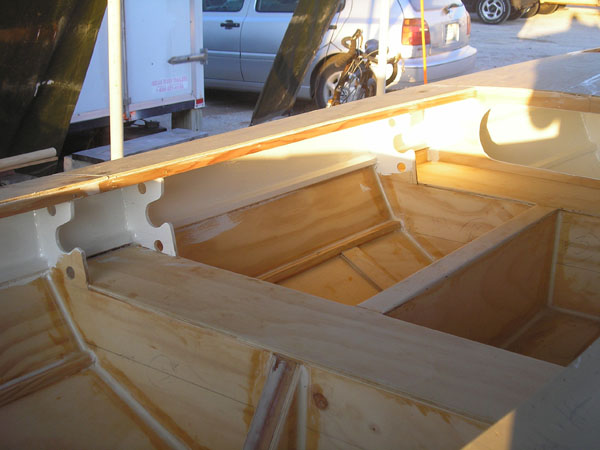
The
fore deck requires small filler pieces to bring the
frame up to deck level
The areas under the side decks are
painted before laying the decks, which are then glued & fastened
All
decking
glued in place
The mast partners must be drilled to the angle of mast
rake using a hole saw with a long guide bitt
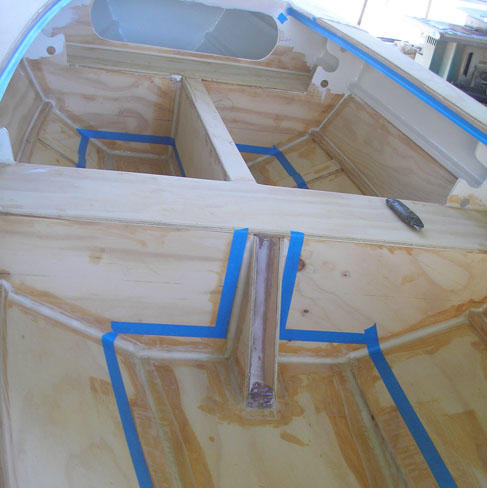
The
hull
is masked offprior to applying Xynole/epoxy on the
decks
The inside of the hull
receives Xynole/epoxy to protect the wet and walk areas

Xynole laid in place (left) and wet out (right)
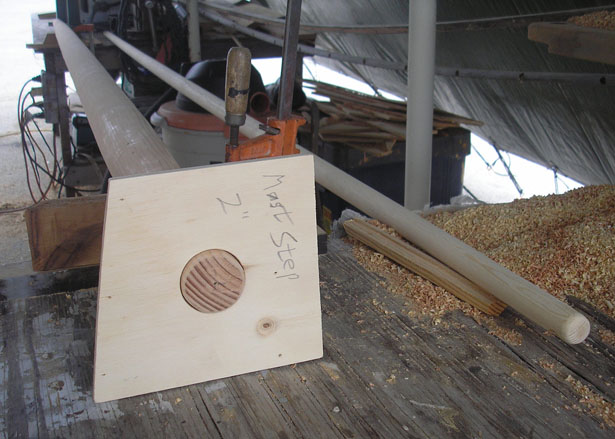
Detail of stem
head and breast
hook
Using a
template to size the base of the mast
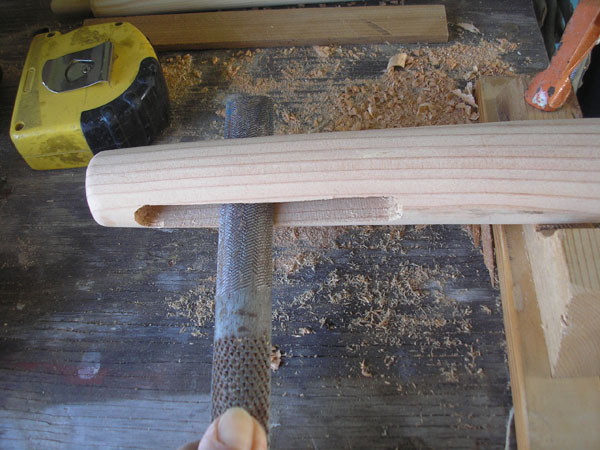
Cutting and finishing the slot for the main and jib haliard sheaves
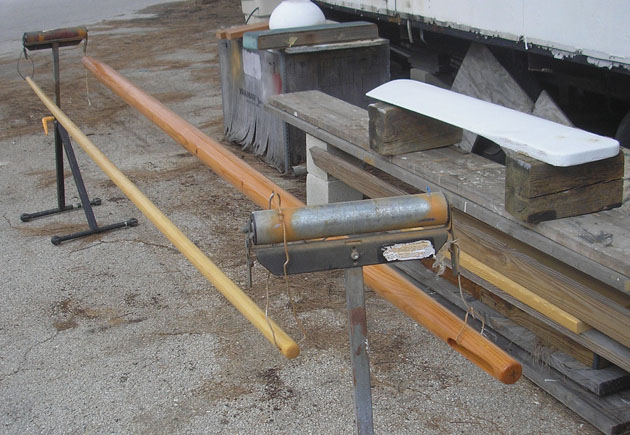
A concave sanding pad made on the table saw for
mast-shaping
The mast
and sprit finished and epoxy
sealed prior to varnish
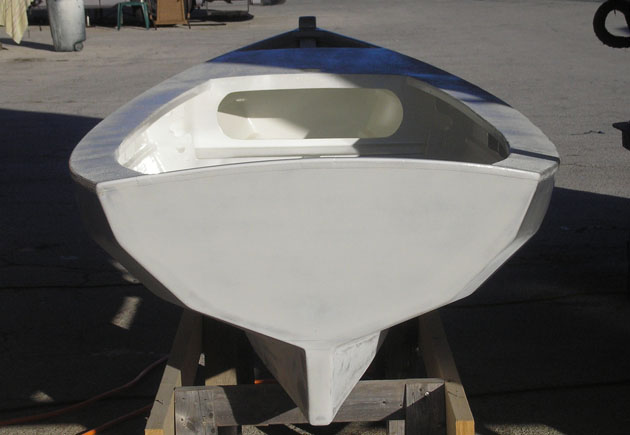
The rudder in
primer
The hull in
primer
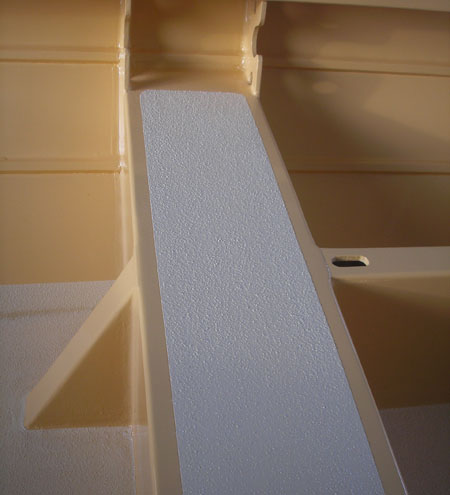
Applying non-skid using epoxy primer and fine sand-blasting sand
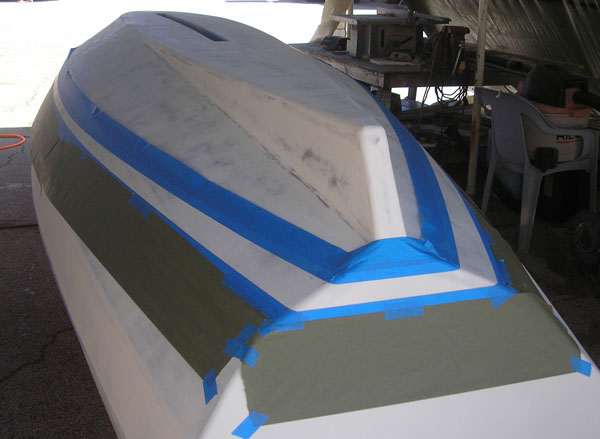
Using battens to establish the boot top
Masking the boot for paint

The Imron
finish painted Sea Bright 14 with teak
rubrails
JERSEY GIRL prior to bottom
paint (Scott Williams photo)
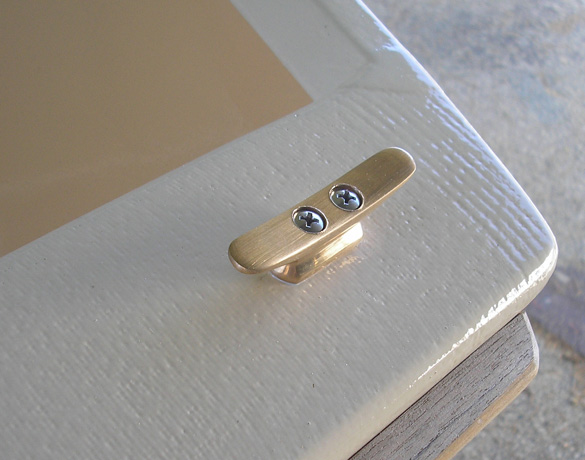
Stern cleat components--backing block is 1/8"
aluminum
plate
Stern
cleat installed
with bedding compound
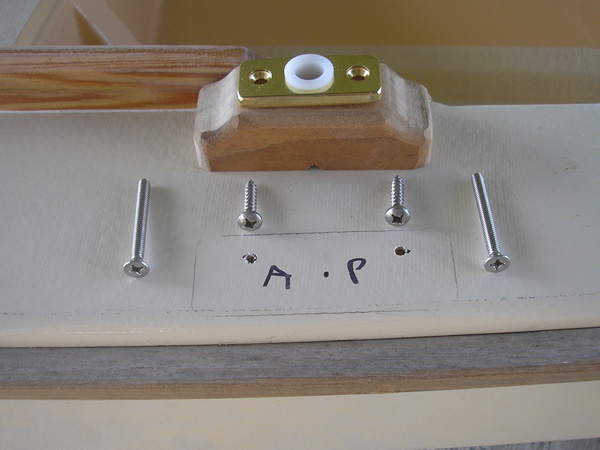
Oarlock gudgeon & teak mounting base with weep hole--the pan head
screws are installed from beneath the deck; the bolts pass through the
gudgeon and the deck
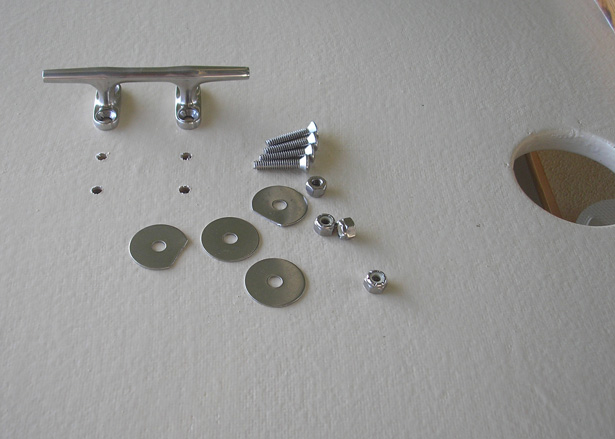
Rowlock gudgeon and base installed
with bedding
compound
Foredeck cleat and
backup fender-washers--the deck centerline is doubled for additional
backup strength

Foredeck
cleats
installed with bedding
compound
Starting the rat-tail cringle for the mains'l peak--I have already made
the sails
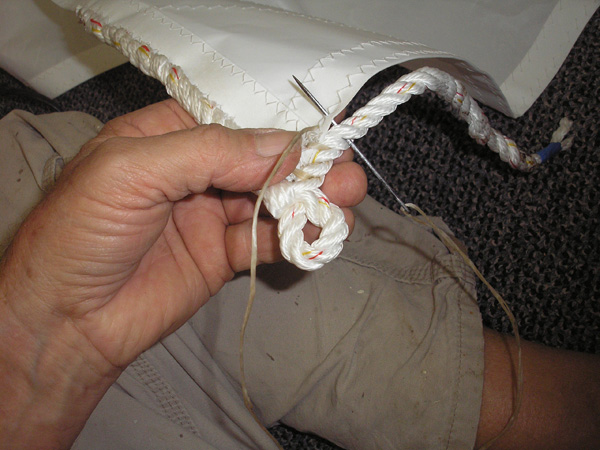
Forming the cringle by unlaying have the rope and starting a
splice After laying up
strands on both sides of the cringle while cutting strands out to form
the tapered rat-tails, the cringle is sewn onto the peak
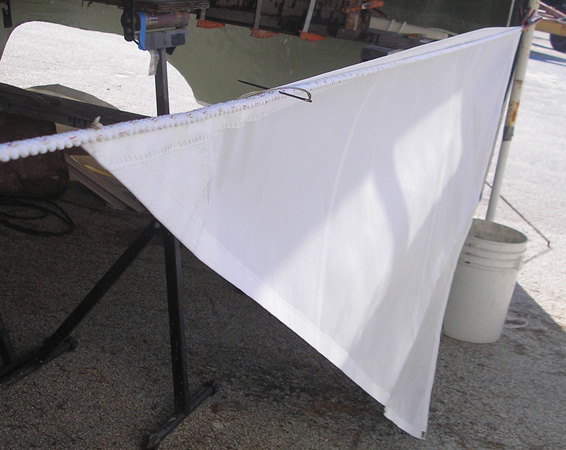
Sewing the jib to the jibstay, which is also the halyard and tack
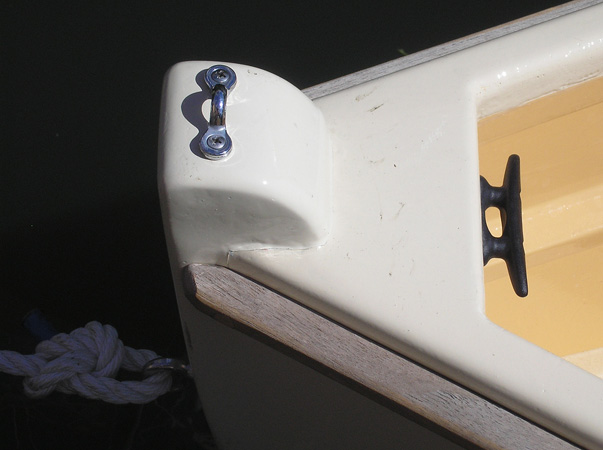
Antifouling paint applied (two
coats)
Bow strap eye for the jib tack; cleat for the tack
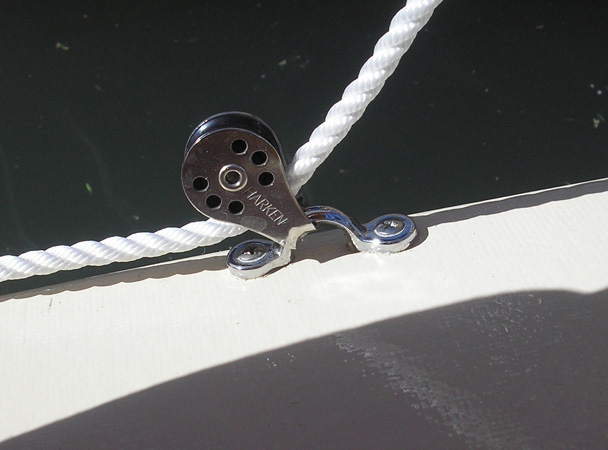
Cleat for the port side jib sheet
Fairlead block for the port side
jib sheet

Rudder
hardware adapted from Schaefer components
JERSEY GIRL with
cypress coamings, rowing hardware, towing eye and cleats--oars are 8'
ash
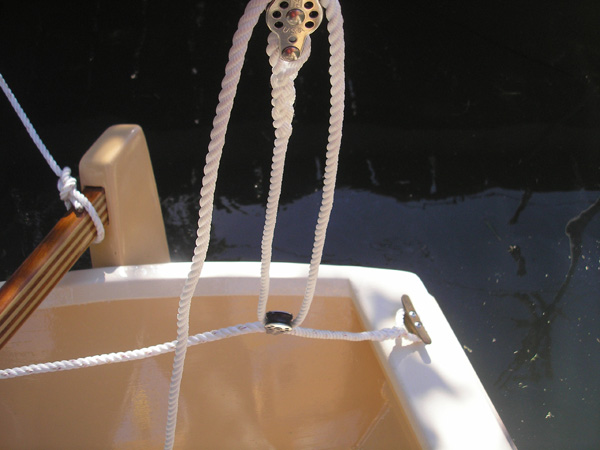
The
mains'l
peak cringle on the sprit
nipple
The main
sheet, which I later relocated to the rudder head, eliminating the rope
traveler

JERSEY GIRL on the trailer

Reuel sailing JERSEY GIRL on Senebec Lake, Union, Maine (Tom Adams
photo)